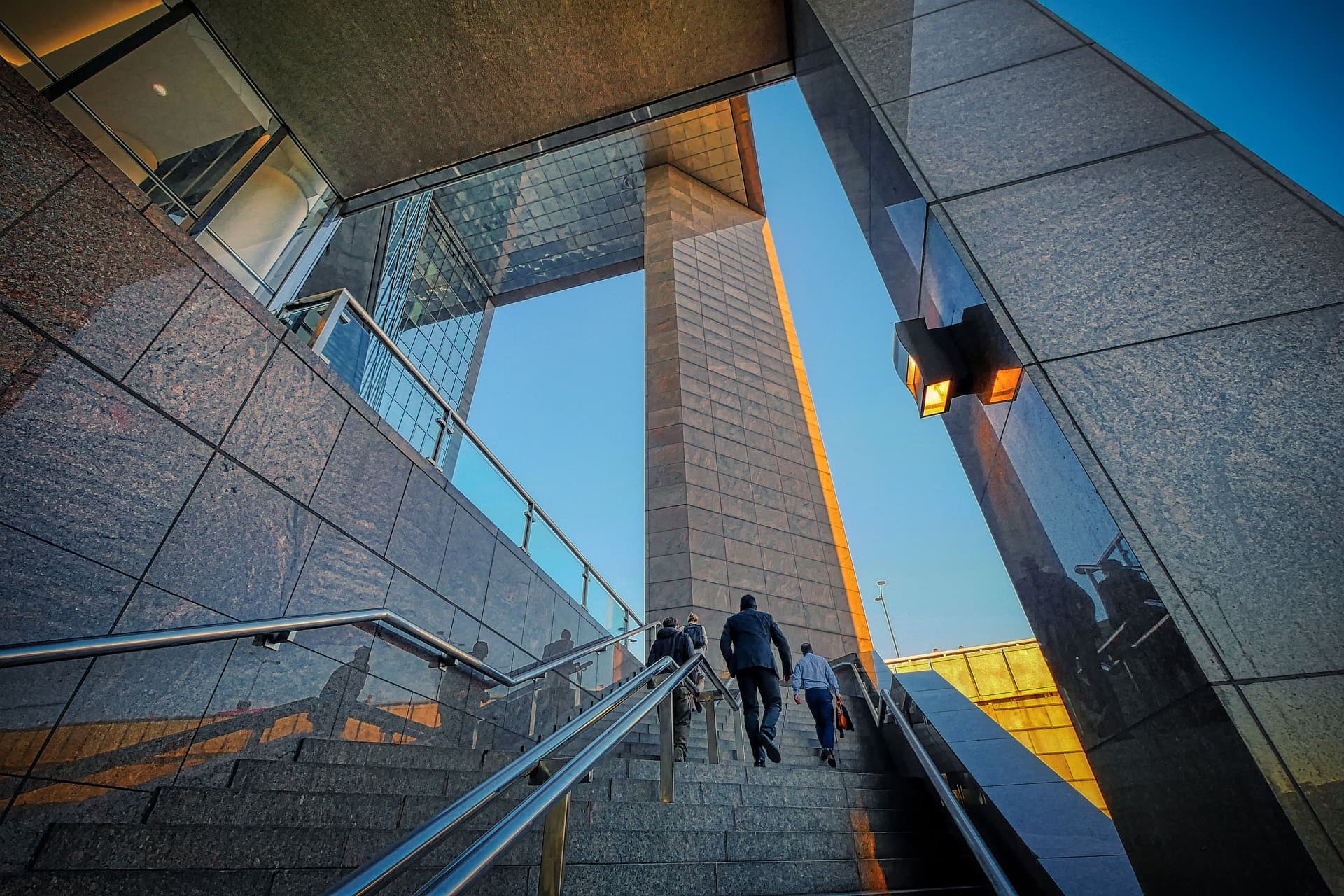
事例: 生産管理運用のシステム化支援
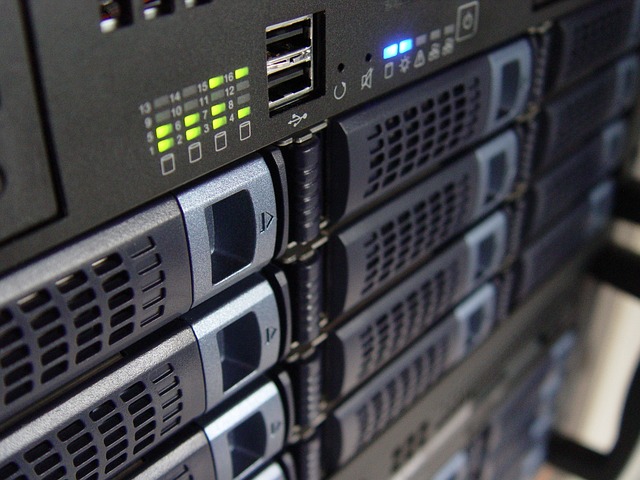
業種
製造業(自動車部品 組立ライン 売上170億円規模)
背景
本社にあるオフコンでメーカから送られる生産計画を受け取り、離れた工場に情報ファイルと組立ラインにラベル情報を送っている。 工場ではメーカからのインライン情報を最終情報として部品の製造と組立てを行い、組立品をラインの製造順番に自動倉庫を使って並べ変へトラックでメーカの製造ラインに合わせ逐次納品が 行われている。 生産計画は長期、中期、短期の受注予測情報とメーカからの直前のライン情報をもとに製造調整を行って運用している。
問題点
- コンピュータシステムが一元管理されていなく、連携が取れていない
- 本社で受取る情報と工場で対応する生産情報にずれが発生している
- 1週間単位での生産計画の調整がしにくい状況
- 各担当者がそれぞれにExcel、Accessによってばらばらに使用している
- 結果的に属人的管理になり全体最適はもとより引継ぎができない
支援内容
- 現状の業務の調査
- 現状の業務運用システムの問題点を明確化
- コンピュータシステムの再検討
- 生産管理システムの統廃合と再構築の検討
- 受注情報に基づいた生産計画、工程指示と納入先ライン生産変動に連動した計画作成支援方法の検討
結果
- 工場側で立てられた生産計画に基づいて、各組み立てラインに対して指示とラベルの発行を実現
- 納入先の製造変動に対して、週間単位で生産数を日割で調整可能とした
- 余分なラベル出力が必要なくなった
- お客様からの指示変更に対して検討容易になった
- 生産管理の情報は工場におかれたサーバで一元管理を実現
- システムのバックアップが明確
- システムのリモートでの管理を実現
- ネットワークの再構を実現